All of the information that is important to know about custom flange
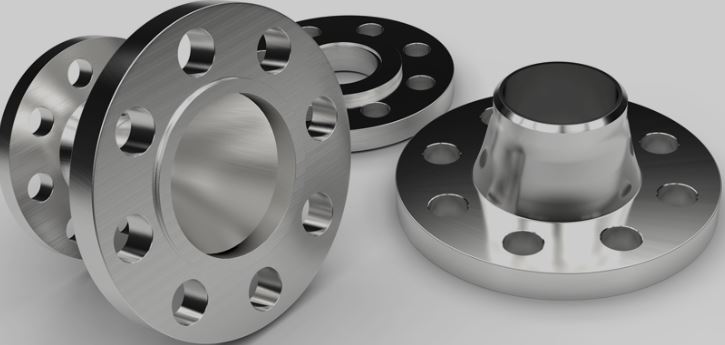
Flange manufacturers on the market in the production of flanges, is to be in accordance with the standard to produce, and also more in accordance with the national standard to produce flanges, that is: in accordance with the national standard requirements of the size, tolerance range, etc. production flange, such a standard flange in use, although also can be used, but more often than not, industrial production requirements of the flange is not the same, so that the flange specifications will also change, such as the Industrial production will not be able to use the standard flange, can only use large flanges; some industrial production can only use smaller flanges to use, so, in the face of such a situation, the standard custom flanges on the market is no longer applicable, can only be customized
As an illustration, a custom slip-on flange is useful because it allows the pipeline to be welded into monoflanges before welding. For the purpose of preventing leakage, it is necessary to provide adequate strength both internally and externally.
When it comes to custom lap joint flanges, the welded flange is comparable to the sliding flange, unless it specifically has a hole and counter bore dimension. By doing so, any flow restrictions are removed, and the ease of operation achieved through the utilization of custom welded flanges is enhanced.
Additionally referred to as shaped flanges, shaped flanges are utilized for the purpose of sealing and fastening connections
-
Despite the fact that processing capacity is not taken into account, the size of profiled flanges is excessively large
-
As a result, the overall processing of profiled flanges must be divided into flaps for the sole reason of transportation
-
Pressure level, material, standards, and other factors are all shaped flanges
-
Steel, carbon steel, alloy steel, and stainless steel make up the majority of the materials
In order to design a flange that is unique to our needs, we need to have a solid understanding of certain essential information. Understanding the type of flange, its size, its pressure rating, and the type of flange face is the first step in comprehending flanges.
We are able to design a flange that not only satisfies but also exceeds your requirements once we have gained an understanding of your needs. Before any significant custom flanges are fabricated, it is necessary to have a thorough understanding of the following considerations. Additional choices include nipoflanges, weldoflanges, expansion flanges, orifices, long weld necks, and reducer flanges. These are just some of the aforementioned alternatives. welded-on-lange
Although it is a combination of a butt weld flange and a branch fitting connection, the Weldoflange is very similar to the Nipoflange in terms of its construction. It is not understood that the Nipoflange is made up of two different products that have been welded together, despite the fact that it is discovered to be a solid single piece of forged steel. In order to install the Nipoflange, the pipe crew must first weld the flange section to the branch pipe flange and then bolt the flange section to the Nipolet section of the equipment that is used to run the pipe. In comparison to standard Nipoflange, reinforced versions of Nipoflange are typically manufactured. This helps to give the reinforced versions of Nipoflanges additional mechanical strength.
For pipelines with a large diameter, the pipe is installed at one end, with a standard butt weld flange, and the other end is a swivel flange. This configuration is used for large diameter pipelines.
A butt weld flange that has a very large bore at the end that is not flanged is typically what is known as an expansion flange.