The Role of the Rotigotine Factory in Medication Safety
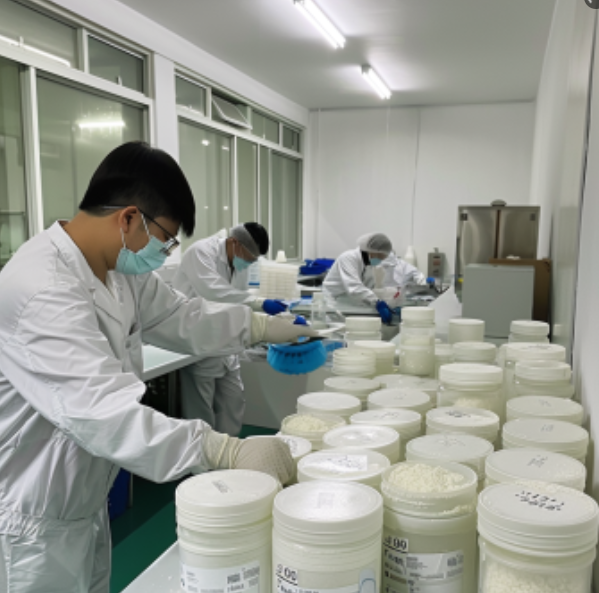
Rotigotine is an important medication used to treat Parkinson's disease and restless legs syndrome. As the manufacturing site for raw materials and finished dosage forms, the Rotigotine factory plays a crucial role in ensuring the medication's quality, safety and effectiveness.
Compliance with Good Manufacturing Practices
Rotigotine factories operated by reputable manufacturers like Neuraxpharm strictly adhere to Good Manufacturing Practices (GMP). GMP regulations cover all aspects of production from facilities, equipment, raw material sourcing, manufacturing processes, testing, and quality controls.
Qualified and Trained Staff
Only properly qualified personnel with relevant expertise, education and ongoing training in GMP are allowed to work in sterile and non-sterile sections of the factory. Their activities are closely monitored.
Facility Design and Maintenance
Rotigotine manufacturing plants are purpose-built with zoning controls to prevent cross-contamination. Utilities, HVAC, cleaning and calibration are validated regularly to ensure environmental conditions support product quality.
Raw Material Controls
Raw materials sourced from approved suppliers meet strict specifications and are tested prior to release and use in production. Their storage prevents mix-ups, contamination and deterioration.
Production Process Validation
Rotigotine manufacturing processes undergo extensive validation studies to demonstrate consistency, reproducibility and control prior to cGMP production. On-going monitoring verifies continued effectiveness.
In-Process and Finished Product Testing
Samples taken throughout production and from final dosage forms are rigorously tested for critical quality attributes like identity, purity, stability and sterility. Only passing batches are released.
Stability Testing Program
Long-term studies conducted under real time/accelerated conditions as per guidelines establish shelf-life and ensure rotigotine retains specifications within expiry dates under recommended storage conditions.
Medical Documentation System
The rotigotine factory maintains records showing adherence to cGMPs and detailed batch documentation permitting full traceability and compliance verification by health authorities.
Environmental Monitoring Program
Air, surface and personnel sampling detect potential contamination issues promptly. Cleaning validation checklists verify disinfection between batches and campaigns.
Change Control System
Any modifications to facilities, equipment, materials or processes undergo formal review and approval to prevent unexpected quality impacts.
Ongoing Audits and Inspections
Regular self-inspections and third-party audits ensure sustained GMP compliance. Health authority inspections further verify rotigotine production meets strict standards for patient safety and product quality.