CNC Machining Design Tips: Enhancing Your Manufacturing Process with Diecasting-Mould
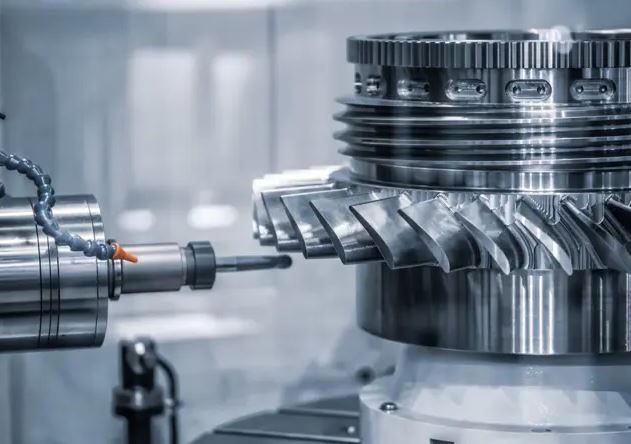
In the ever-evolving world of manufacturing, CNC machining stands as a cornerstone of precision and efficiency. However, to fully leverage the capabilities of CNC machining, it's essential to follow best design practices. This article delves into practical design tips for CNC machining, ensuring optimal performance, cost-efficiency, and quality. By integrating these tips and partnering with a reliable CNC machining service supplier like Diecasting-Mould, you can significantly enhance your manufacturing process.
Computer Numerical Control (CNC) machining is a subtractive manufacturing process that uses computer-controlled tools to remove material from a workpiece. This technology offers unmatched precision, allowing for the creation of complex parts with tight tolerances. CNC machining is used across various industries, from aerospace to medical devices, owing to its ability to produce high-quality parts efficiently.
Key Advantages of CNC Machining
-
Precision and Accuracy: CNC machines can produce parts with exceptional accuracy, often within microns, making them ideal for detailed and intricate designs.
- Repeatability: Once a design is programmed, CNC machines can produce identical parts consistently, ensuring uniformity across production runs.
- Flexibility: CNC machines can work with a wide range of materials, including metals, plastics, and composites, providing versatility in manufacturing.
- Efficiency: CNC machining reduces manual intervention, leading to faster production times and lower labor costs.
- Complex Geometries: CNC machines can handle complex geometries that would be challenging or impossible with manual machining.
Essential CNC Machining Design Tips
To optimize your designs for CNC machining, consider the following tips:
1. Choose the Right Material
Material selection is crucial in CNC machining. Each material has unique properties that affect machinability, strength, and finish. Common materials include aluminum, steel, titanium, and various plastics. Understanding the properties of your chosen material can help in selecting the appropriate cutting tools and machining parameters.
- Metals: Aluminum is popular due to its excellent machinability and lightweight. Steel offers superior strength but requires more robust tooling.
- Plastics: Materials like ABS and polycarbonate are easier to machine and suitable for prototypes and lightweight parts.
2. Optimize Part Geometry
Designing for CNC machining requires attention to part geometry. Simpler geometries reduce machining time and cost. Here are some guidelines:
- Avoid Deep Cavities: Deep cavities require longer tools, which can lead to deflection and vibration. Instead, design with a maximum depth of 4 times the tool diameter.
- Maintain Uniform Wall Thickness: Uniform wall thickness reduces stress concentration and deformation during machining.
- Include Fillets: Adding fillets to internal corners helps in reducing stress and tool wear. A fillet radius of at least 1/3 of the cavity depth is recommended.
3. Tolerances and Surface Finish
Specifying the right tolerances and surface finish is vital for both functionality and cost. Tighter tolerances increase machining time and cost, so it's crucial to balance precision with practicality.
- Standard Tolerances: Use standard tolerances (e.g., ±0.1 mm) for non-critical dimensions to reduce costs.
- Surface Finish: Specify the required surface finish. While a smooth finish enhances appearance and performance, it may increase machining time.
4. Threading and Tapped Holes
Threaded and tapped holes are common in CNC machined parts. Proper design ensures ease of manufacturing and assembly:
- Standard Threads: Use standard thread sizes to simplify tool selection and reduce costs.
- Hole Depth: For blind holes, the thread depth should not exceed 3 times the hole diameter to avoid tool breakage.
- Chamfers and Deburring: Add chamfers to hole entries and deburr edges to facilitate assembly and improve safety.
5. Fixture Design
Effective fixture design is essential for holding parts securely during machining. Proper fixturing reduces vibrations, improves accuracy, and ensures safety.
- Custom Fixtures: Design custom fixtures for complex parts to improve stability and reduce setup time.
- Accessibility: Ensure fixtures allow tool access to all required surfaces without obstruction.
Partnering with Diecasting-Mould for CNC Machining Services
Choosing the right CNC machining service supplier is crucial for achieving high-quality results. Diecasting-Mould is a leading provider of CNC machining services, offering expertise, advanced technology, and exceptional customer support.
Why Choose Diecasting-Mould?
- State-of-the-Art Equipment: Diecasting-Mould utilizes the latest CNC machines and software, ensuring precision and efficiency in every project.
- Experienced Team: Our skilled engineers and machinists bring years of experience to each project, delivering top-notch results.
- Comprehensive Services: From prototyping to large-scale production, Diecasting-Mould offers a full range of CNC machining services to meet diverse needs.
- Quality Assurance: Rigorous quality control measures ensure that each part meets exact specifications and industry standards.
- Customer Support: Our dedicated customer support team is always available to assist with any queries and ensure a smooth process.
Steps to Work with Diecasting-Mould
Engaging with Diecasting-Mould for your CNC machining needs is straightforward:
1. Initial Consultation
Contact us to discuss your project requirements. Our team will provide insights and recommendations based on your specifications.
2. Design Review and Optimization
We review your CAD files and suggest optimizations to improve manufacturability and reduce costs.
3. Quotation and Order Confirmation
Receive a detailed quotation outlining the project scope, costs, and timeline. Once approved, we proceed with the order.
4. Production and Quality Control
Our team executes the machining process with precision. Each part undergoes thorough quality checks to ensure compliance with your specifications.
5. Delivery and Support
We deliver the finished parts to your location. Our team remains available for any post-delivery support or adjustments.
Future Trends in CNC Machining
The CNC machining industry is continuously evolving, driven by technological advancements and changing market demands. Here are some trends shaping the future:
- Automation and AI: Integration of AI and automation is enhancing efficiency and reducing human intervention in CNC machining processes.
- 5-Axis Machining: The adoption of 5-axis CNC machines is increasing, allowing for more complex geometries and reducing the need for multiple setups.
- Advanced Materials: Innovations in material science are expanding the range of machinable materials, including composites and advanced alloys.
- Smart Factories: The concept of smart factories, where CNC machines are integrated into a fully digitalized production environment, is gaining traction.
Effective CNC machining design is critical for optimizing manufacturing processes, reducing costs, and ensuring high-quality output. By following the design tips outlined in this article and partnering with a reputable CNC machining service supplier like Diecasting-Mould, you can achieve superior results in your projects. Embrace the future of manufacturing with advanced CNC machining solutions and stay ahead in the competitive landscape.