From Scratch to High Frequency: The Evolution of TIG Welding
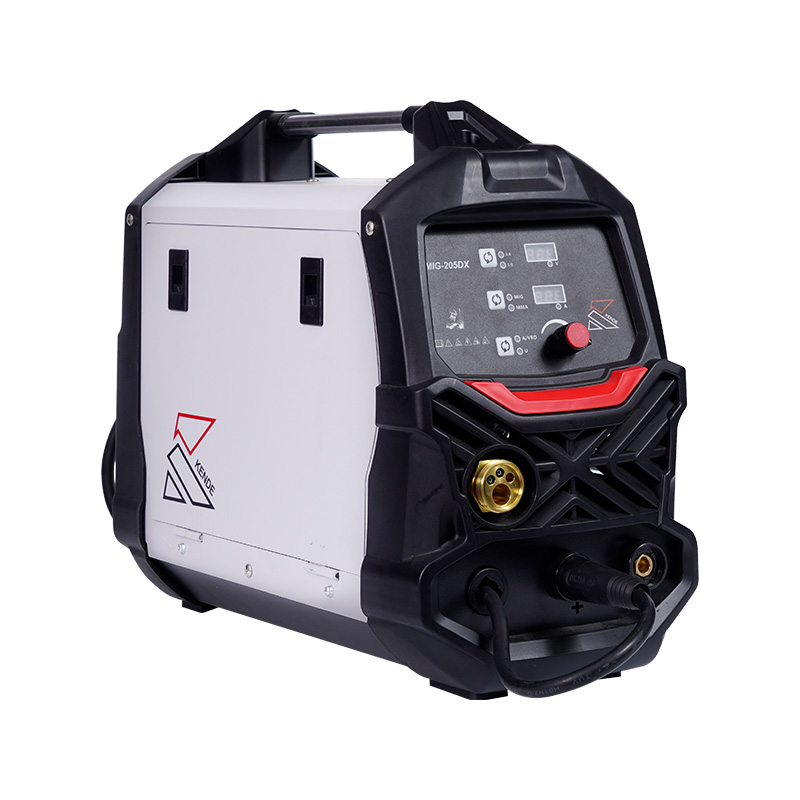
The high frequency TIG welder utilizes a high-frequency electrical signal to initiate the welding arc. This method allows for a non-contact arc start, which is particularly beneficial when working with sensitive materials like aluminum. In contrast, traditional TIG welders often rely on a scratch start or lift arc method, which can cause contamination of the weld area and affect the overall quality of the weld. The ability of the high frequency TIG welder to create a clean arc without touching the workpiece minimizes the risk of defects, making it a preferred choice for high-precision applications.
It also can be used for a wide range of materials, including stainless steel, aluminum, and even exotic metals like titanium. This flexibility is crucial in industries such as aerospace and automotive, where different materials are frequently used. Traditional TIG welders, while effective, may not provide the same level of adaptability, often requiring additional equipment or settings adjustments to handle various materials.
Moreover, the high frequency TIG welder offers improved arc stability. The high-frequency signal helps maintain a consistent arc, even in challenging conditions. This stability translates to better control over the welding process, allowing for more intricate and detailed work. Welders using a high frequency TIG welder can achieve finer weld beads and more aesthetically pleasing results, which is particularly important in applications where appearance matters.
- Art
- Causes
- Crafts
- Dance
- Drinks
- Film
- Fitness
- Food
- Jocuri
- Gardening
- Health
- Home
- Literature
- Music
- Networking
- Alte
- Party
- Religion
- Shopping
- Sports
- Theater
- Wellness
- Social