Circular Systems: Bridging Sustainability and Affordability in Eco-Straws
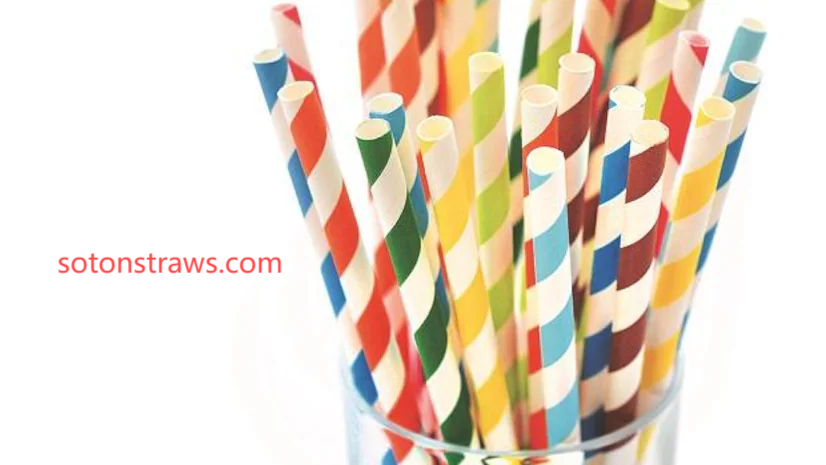
As global industries intensify their pursuit of sustainable alternatives, eco-friendly straws Factory operations are navigating a complex landscape of innovation and regulatory hurdles. Advanced bio-based materials like PHBH (polyhydroxybutyrate-co-hexanoate) and PHA (polyhydroxyalkanoate) are redefining biodegradability standards, offering rapid decomposition in marine and terrestrial environments without microplastic residue. These materials outperform traditional PLA in heat resistance and structural integrity, making them ideal for hot beverages and demanding applications. However, scaling production while balancing cost and compliance remains a critical challenge .
The promise of next-gen biopolymers lies in their environmental performance. PHA, derived from renewable resources like canola oil, breaks down into benign byproducts within months in marine settings, supported by bacterial activity . Similarly, novel composites blending agricultural waste—such as sugarcane bagasse with limestone—achieve biodegradability while enhancing soil quality post-decomposition . These innovations address consumer demands for guilt-free disposables and align with policies like the EU’s Circular Economy Action Plan. Yet, industrial adoption faces steep barriers. Microbial fermentation processes required for PHA production demand specialized infrastructure, driving upfront capital costs. Bio-based straws currently cost multiples of conventional plastics, limiting accessibility for price-sensitive markets .
Regulatory fragmentation further complicates scalability. Divergent certification frameworks—such as Europe’s EN13432 for industrial compostability and ASTM D6400 in the U.S.—create compliance bottlenecks for exporters. Factories must navigate overlapping standards, often investing in dual certifications or modular production lines to serve regional markets . Collaborative R&D initiatives, however, are easing this burden. Cross-border partnerships enable technology sharing, such as optimizing fermentation yields or streamlining biodegradation testing protocols, reducing time-to-market for new materials .
To mitigate costs, manufacturers are adopting circular production models. Closed-loop systems recover post-industrial biopolymer waste for reuse, while renewable energy integration lowers carbon footprints. For instance, solar-powered facilities in Southeast Asia offset energy-intensive sintering processes, aligning with carbon tariffs like CBAM . Concurrently, blockchain traceability ensures transparency across supply chains, verifying sustainable sourcing for eco-conscious brands .
Consumer education is equally vital. Certifications like the “Seedling” mark and BPI labels provide tangible proof of biodegradability, building trust in markets wary of greenwashing. QR codes linking to decomposition timelines or material origins further empower buyers to make informed choices .
click sotonstraws.com to reading more information