Regulation Techniques for Crushing Ratio and Output Particle Size in Custom Mobile Impact Crushers
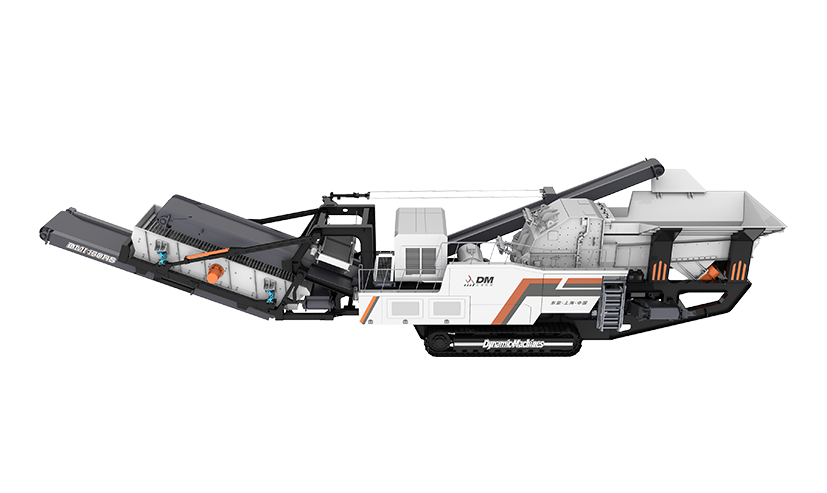
In the world of crushing technology, Custom Mobile Impact Crushers (CMICS) are designed to provide high flexibility and efficiency in the processing of various materials. The ability to adjust the crushing ratio and the finished product's particle size is a critical feature that enables these crushers to cater to diverse applications and specific customer requirements. This article delves into the intricacies of how to regulate the crushing ratio and particle size in Custom Mobile Impact Crushers to ensure optimal performance.
The crushing ratio, which is the ratio of the feed size to the output size, is a fundamental factor in determining the efficiency and output of a Custom Mobile Impact Crusher. A higher crushing ratio indicates a greater reduction in size, which can be beneficial for certain applications but may also lead to increased wear on the crusher components if not properly managed.
Adjusting the crushing ratio in a Custom Mobile Impact Crusher involves manipulating several parameters, including the setting of the impact bars, the speed of the rotor, and the feed material's size distribution. By altering the spacing between the impact bars and the anvils, operators can control the size of the discharge opening, which directly influences the particle size of the crushed material. A smaller gap results in finer particles, while a larger gap allows for coarser particles to pass through.
The rotor speed is another critical factor that impacts the crushing ratio and particle size. A faster rotor speed increases the kinetic energy of the impacting hammers, leading to a higher crushing ratio and smaller particle sizes. However, it also increases the risk of overcrushing and excessive wear on the crusher components. Conversely, a slower rotor speed results in a lower crushing ratio and larger particle sizes but reduces wear and tear.
The feed material's size distribution also plays a significant role in the crushing process. Feeding the Custom Mobile Impact Crusher with a more uniform material size can lead to a more consistent product size and reduce the risk of blockages. On the other hand, a varied feed size can lead to a wider range of particle sizes in the final product, which may or may not be desirable depending on the application.
In addition to these physical adjustments, modern Custom Mobile Impact Crushers often come equipped with advanced control systems that allow for precise regulation of the crushing process. These systems can automatically adjust the settings based on real-time feedback from sensors monitoring the crusher's performance. This technology not only optimizes the crushing ratio and particle size but also enhances the overall efficiency and longevity of the crusher.
Maintenance and regular inspection of the Custom Mobile Impact Crusher are also crucial for maintaining optimal crushing performance. Worn or damaged components can significantly affect the crusher's ability to achieve the desired crushing ratio and particle size. By replacing impact bars, anvils, and other wear parts promptly, operators can ensure that their Custom Mobile Impact Crusher continues to operate at peak efficiency.
In conclusion, regulating the crushing ratio and particle size in Custom Mobile Impact Crushers is a complex process that involves a combination of physical adjustments, advanced control systems, and diligent maintenance. By understanding and applying these techniques, operators can tailor the performance of their Custom Mobile Impact Crusher to meet the specific demands of their applications, resulting in improved efficiency, reduced downtime, and increased profitability.
Mobile Impact Crusher Feed Particle Size: ≤650mm
Processing Capacity: 80-360t/h
Machinery Weight: 45-62t